About Us
About the company
American Radionic Co., Inc. located sixty miles south of Jacksonville in Palm Coast, Florida is a leader in metallized film capacitor technology. American Radionic relocated its entire base of operations from Danbury, Connecticut to Florida in July 1987. As a major supplier for over thirty-five years to the “big” three domestic automobile companies, the move allowed American Radionic to expand its production facilities and be a leader in applying lean manufacturing principles. The entire facility was restructured using lean manufacturing practices to meet our customers’ stringent demands and keep American Radionic competitive with a high-quality product in the marketplace. All capacitors to this day are 100% designed and manufactured in Palm Coast.
American Radionic and its AmRad division hold numerous patents and trademarks on its film capacitor designs. They maintain a technology and licensing group for collaborative work with worldwide capacitor manufacturers and complete “turn-key” services.
Recent innovative products have included the Patented Turbo®200 Universal Replacement Service Capacitor, which uses the American Radionic Patented Ultramet Capacitor design technology. The Ultramet is the world’s first multiple-metalized film capacitor derived from a single continuous winding.
The Turbo®200 has completely revolutionized the HVAC service industry and its approach to service repair work. One capacitor can be used to replace up to 200 values, thus eliminating the need to maintain large inventories of capacitors. Most importantly, the serviceman is assured of having a replacement part at the time of service. An entire family of Turbo’s has since been introduced.
A Custom Turbo intended for multiple OEM applications can replace a range of part numbers. A Custom Turbo can operate up to six (or more) electric motors at once. Engineers and purchasing can take advantage by consolidating part numbers and reducing assembly costs. A Custom Turbo will also meet the demands when there is an emergency inventory shortage. Simply use the jumper wires and create the capacitor value needed.
Eighty-five years of capacitor engineering and manufacturing highly qualifies American Radionic and its industry-experienced personnel to meet the needs of its customers. Complete engineering support for the design, [including extensive testing to customer specification], testing (using in-house high-voltage test equipment), and prototype sampling is readily available.
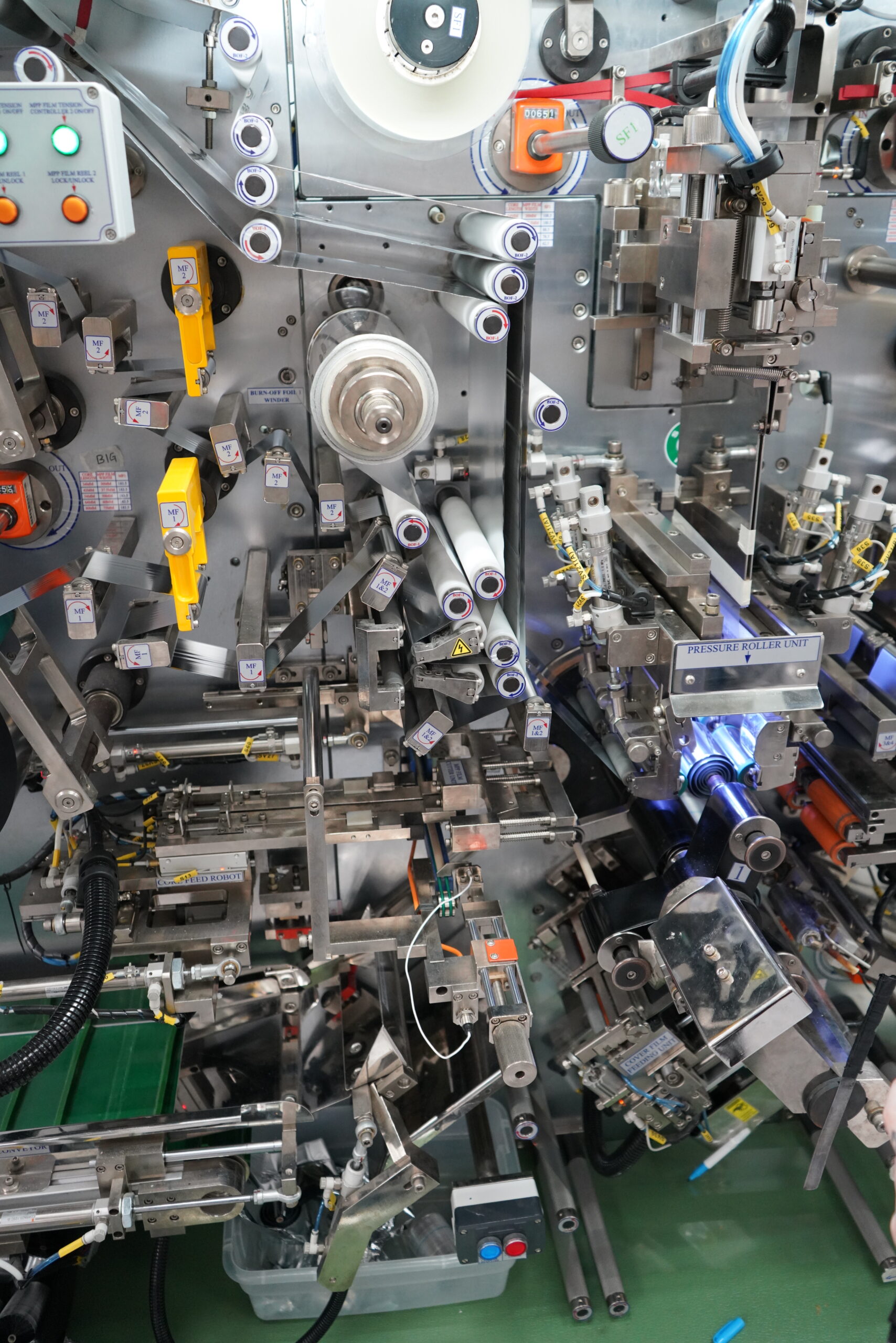
Support American
Manufacturing
As an American manufacturer, we have extended a mark of recognition to our supporters.
Our AmRad Authorized Platinum Wholesalers carry our Turbo 200®, Turbo 200®X, Turbo Easy-Start® 5 (TES5), and USA Capacitors in substantial quantities.
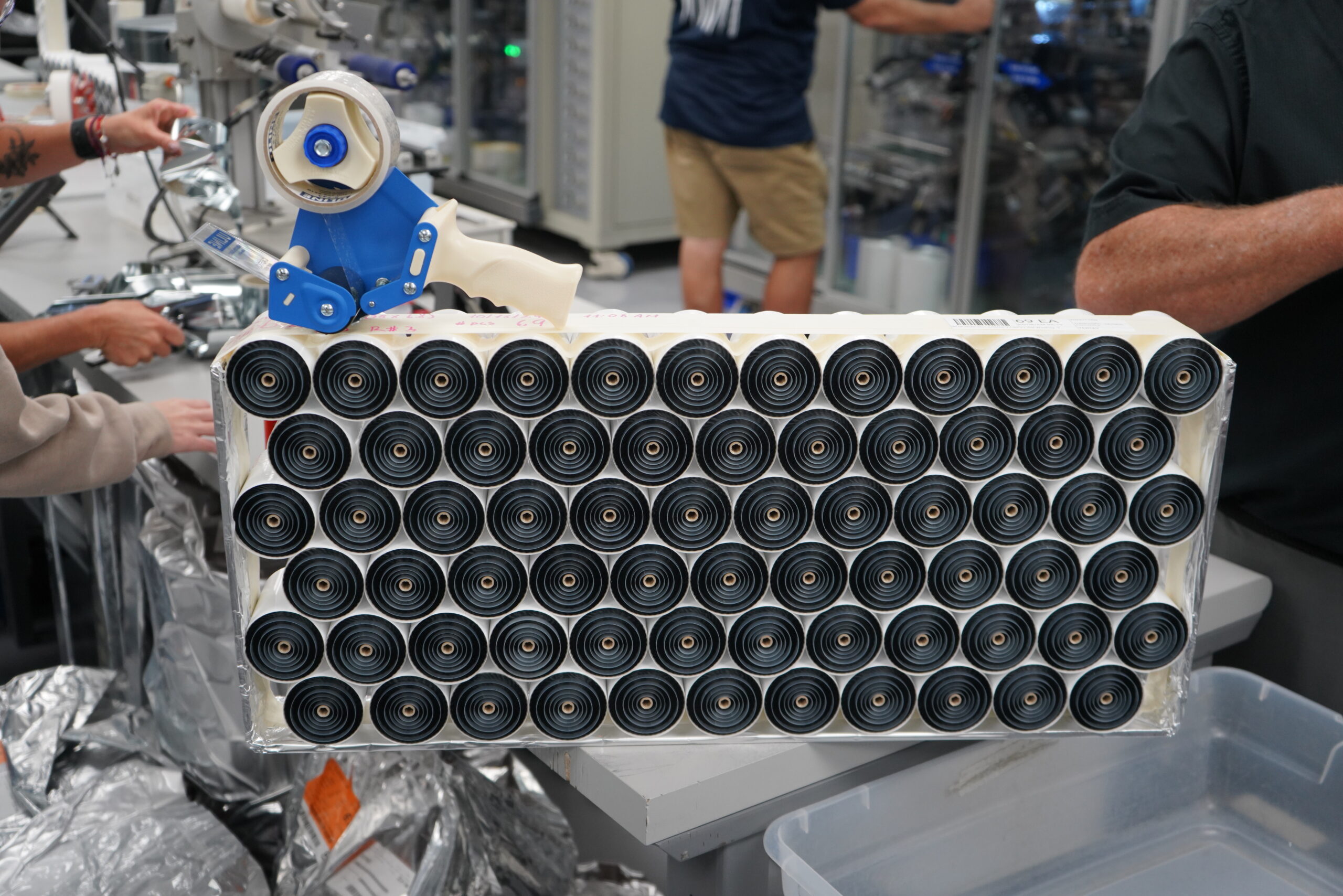
NEWS
July 1, 2020
Global, The Source has acquired AmRad Engineering. Both proud, American, Family-Owned Companies have come together as one.
Global and AmRad have been dating for fifteen years and thought it was time to make it official! Their union secures the future of American Manufacturing and the American Worker.
These two families will blend together seamlessly, with each business continuing to operate as usual. Global is happy to announce, AmRad President, Turbo 200® inventor and patent designer, Robert Stockman, will be assuming a consulting role and AmRad’s dedicated employees are happy to continue working with Global.
For more information, visit Global The Source at www.globalthesource.com or call 800.531.5967.
March 31, 2015
THOUSANDS IN USE THROUGHOUT THE COUNTRY!
That’s right…with the TURBO®200 you’ll always have the correct
dual value motor-run capacitor when you need it!
SAVE MONEY & SPACE – REDUCE INVENTORY – MORE SERVICE CALLS PER DAY
MOST IMPORTANTLY – EARN MORE MONEY!!
For reliability and performance, the Turbo®200, 200X & the Mini meet the SAME UL 810, 10,000 AFC PROTECTED (amp fault current) safety standards as required for all original equipment motor-run capacitors.
DON’T BE MISLED. Only Amrad’s Turbo®200 series has this critical UL 10,000 AFC: PROTECTED certification.
FOR AN AUTHORIZED WHOLESALER NEAREST YOU, PLEASE
CONTACT GLOBAL AT 800-531-5967 OR AMRAD AT 800-445-6033
Distributed to the U.S. HVAC Service Industry Exclusively by Global The Source
For specific information regarding wholesalers/supply houses call: 1-800-531-5967
Outside the U.S., contact AmRad’s International Sales Group at: 1-407-362-1854 (8 AM to 6 PM, EST).
The TURBO®200 is produced under one or more American Radionic patent numbers:7,474,519; 7,423,861; 7,203,053; 6,014,308; 5,313,360; 4,312,145; 4,312,027; 4,028,595; 3,921,041 Additional US and foreign Patents Pending.
THE TURBO®200 is designed, developed and manufactured by
American Radionic Co, Inc., Palm Coast, Florida USA
March 31, 2015
Palm Coast, Florida — American Radionic, Co., Inc., is pleased to announce that the United States Patent & Trademark Office recently issued U.S. Patent No. 7,203,053. This patent marks an important step in American Radionic’s ongoing efforts to protect its intellectual property rights.
The ’053 patent, entitled, “Capacitor For Multiple Replacement Applications,” is the product of American Radionic’s novel engineering work behind its Turbo200® products. American Radionic has been an innovator in the capacitor field throughout its sixty-seven year history, and is committed to obtaining patent protection for its innovations.
Turbo200® products can provide up to 200 possible capacitance values, eliminating the need for technicians to bring a vast inventory of capacitors into the field to repair air conditioners. The Turbo 200® line of products includes the Turbo200®, Turbo200®X, Turbo200® Mini and the Turbolytic™. American Radionic’s Turbo200® products are made in the U.S.A.
All Turbo200® products are certified by Underwriters Laboratories, Inc. (UL) under the UL 810 standard as protected to 10,000 AFC (available fault current). U.S. manufacturers of air conditioning and similar equipment require that capacitors in those products provide this level of protection. American Radionic is proud to offer capacitors that meet this high standard. American Radionic has carefully cultivated its reputation for high quality, stringent testing, and appropriate certification for its products to ensure their safe performance.
The Turbo200® is available at more than 2,000 wholesalers throughout the United States and Canada and is exclusively distributed to the U.S. HVAC industry by Global The Source. For specific information regarding wholesalers/supply houses call:(Global) 1-800-531-5967 or American Radionic at 1-800-445-6033.
Outside the U.S., contact AmRad’s International Sales Group at: 1-407-362-1854 (8 AM to 6 PM, EST) or 1-386-445-6000.
The TURBO200® is produced under one or more American Radionic patent numbers: 3,921,041; 4,028,595; 4,312,027; 4,312,145; 5,313,360; 6,014,308; 7,203,503. Additional US and foreign Patents Pending
HISTORY
2007
(Jan) AmRad introduces the Turbo®Meter—a dual screen capacitance meter for use with the Turbo®200 product line. Allows the contractor to see both fan and compressor values at the same time as the Turbo®200 is installed.
2006-12
(Dec) Turbo®200 is American Radionic’s United States Patent office trademark registration number 3,141,014.
2006-10
(Oct.) AmRad Engineering has developed the Turbolytic®200, a universal replacement capacitor using advanced thin-film technology. This device, which has six separate capacitors in a single continuous winding and uses jumper wires to “create” numerous different values. The Turbolytic®200 has broad implications for the “industrial-based” service equipment industry as well as for OEMs. The Turbolytic®200 encompasses 20 mfd to 450 microfarads. In the months ahead, we expect to cover the rang from 100 mfd through 1500 microfarads.
2006-08
(Aug.) American Radionic has re-established its Precision Capacitor Division. At this time, particular emphasis is being placed on high microfarad film dielectric capacitors. These range from 100 microfarads to 2,500 microfarads. Historically, this has been the realm of electrolytic capacitors but these have numerous short comings in many modern applications. With recent advances in thin-film capacitor dielectric products as well as in metallizing (coating) capabilities along with AmRad’s advanced capacitor winding machine technology, a whole new product line is being developed. These capacitors (HMFC series — high microfarad film capacitors) have vast implications for power supplies, both industrial and military.
AmRad Engineering introduces the world’s first dual screen capacitance meter for the simultaneous reading of dual capacitor values. This device is extremely helpful to a service technician when “setting” up (that is, wiring), theTurbo®200 Series of Universal Replacement capacitors. Patents have been applied for this new and very unique device.
2005-10
(Oct.) Another item is added to the Turbo®200 line of universal capacitors. It is the Turbo®200 Mini. A small capacitor to be used for single value (“fan-sized”) capacitors. [Note: Used mainly on air handling units for use with fan motors.]
2005-06
(June) AmRad Engineering adds another product to the Turbo line with the introduction of the Turbo™200X. This device is targeted to the higher range of microfarad values ( 70mfd to 97.5mfd ) used in conjunction with scroll compressor-based air conditioning equipment.
2005-02
(Feb.) The AmRad Division introduces the Turbo®200 Universal Service Capacitor at the ASHRAE (AHR) show in Orlando, Florida. This device allows an air conditioning service contractor to replace any one of the 200 different single and dual value motor-capacitors used in air conditioning equipment. It was chosen as one of the most significant new items at that show.
An extensive patent program has been established around this new device.
2002
Super Mighty Met.
2001
Patent No. 6,313,978, KF711 receives U.S. Patent.
2000
(Jan.) United States Patent No. 6.014.308 is issued to American Radionic for its trademarked LG22™ special, high viscosity encapsulating fluid.
1999-12
AmRad Engineering introduces the KF711 series of motor-run capacitors. This is a plastic cased impact resistant, fluid filled component which retains the same performance characteristics as the metal can version. This series utilizes the very unique Dual Chamber Design (patent pending).
1999-11
American Radionic again receives Friedrich Air Conditioning Company’s
1999
Outstanding Supplier Award.
1998-10
(Oct.) American Radionic develops a special high viscosity encapsulating fluid offering far superior life test properties – LG22™
1998
Headquarters and Manufacturing hub of American Radionic, currently employs 150 people. AmRad Engineering Division works extensively in the 60Hz voltage range of 120VAC to 440VAC gearing to the appliance field. The products manufactured range from single and multiple value (Ultramet) capacitors for noise-free fan motor switching to single and dual-value metallized polypropylene capacitors for motor-run and HID lighting applications. High volume production as well as “short-runs” can readily be accommodated. Our extensive association with the largest manufacturing companies in the world has led us into the most modern concepts of “lean production”.
Our Engineering and Mechanical Design Departments have developed advanced techniques of mechanization and automation never before seen in file dielectric capacitor facilities. Data acquisition with constant inputs have allowed us to meet the challenges of the late 1990’s and beyond. In the last few years, American Radionic Company has embarked on an expansion program and sales have increased the rate of 33% per year. New markets have opened up and continuous growth is expected in the years ahead.
1996
(Dec.) A new facility for the manufacture of AC rated motor-run capacitors (370VAC, 440VAC) in Fort Smith, Arkansas is now “on-line”. This plant will incorporate the latest in automated and “lean production” concepts.
American Radionic Company’s Technology Transfer Group has been asked to design a turnkey facility (outside the United States) for the high volume production of AC rated motor-run capacitors.Friedrich Air Conditioning of San Antonio, Texas, a world leader in air conditioning equipment has selected American Radionic Company as a recipient of the “1995 FRIEDRICH OUTSTANDING SUPPLIER AWARD”. UNISEAL™ – A newly developed proprietary technique (patent applied for) which allows an outer plastic enclosure to be incorporated into the capacitor during the initial winding process. Provides very significant savings in labor and materials.
Month after month, American Radionic continues to provide “ZERO DEFECT” products to the appliance industry through the concepts of “lean manufacturing.”
1994
Once again, Friedrich Air Conditioning of San Antonio, Texas, a world leader in air conditioning equipment has selected American Radionic Company as a recipient of the “1994 FRIEDRICH OUTSTANDING SUPPLIER AWARD”.
AmRad Engineering Inc., the AC Motor Run Capacitor Division, announces the introduction of Bar Code Labeling on all capacitor labels and packaging. This is an industry first and has been instituted across the line for all AC Motor Run Capacitors.
The U.S. Patent Office issues Patent No. 5,138,519 for the Twister™ Capacitor. This is targeted to the appliance service industry as well as for certain OEM applications. The Twister allows a user to permanently alter the value of a capacitor by turning the terminal one-quarter of a turn. This is the first time that the terminal has ever been used as a switch. There has been tremendous interest in this product throughout the world because it has such great potential to reduce inventory. Anticipated market $25,000,000 per year.
U.S. Patent No. 5,001,597 – Describes a technique of mounting a large capacitor by utilizing the plastic core on which it has been wound. Heretofore, physically larger components required extensive and expensive hardware to mount in equipment. This technique, known as the Axilok™ provides an easy, low cost, simple and totally reliable system of mounting these parts. It is now being used extensively in capacitor based charging circuits and power supplies. introduction of the Mighty-Met™ Capacitor. Using computer analysis to study volumetric efficiencies in the design of AC rated, oil-filled capacitors, it was determined that the most efficient internal construction of a 370VAC (oval base) capacitor up to five microfarads would be by mounting the winding element transversely. This reduces wasted internal volume, can height, etc. Later this would become the standard in the industry.
A decision is reached to enter AC oil (metal can) capacitor market, estimated to be about $200 million worldwide. After ten years of providing technology to companies in this industry and not wanting to compete with licensees, American Radionic decided to develop a niche in this vast potential market. A separate operating division was structured to manufacture this capacitor type, AmRad Engineering Inc. A second building was purchased shortly thereafter.
1989
Ford Motor Company awards Q1 status for the capacitors which are supplied for noise suppression. Japanese companies could not displace American Radionic Co. in the automobile industry. The on-going road testing of automotive electrical products results in an extremely significant development – a high temperature (300°F) capability noise-suppression capacitor using a polyethylene terephthalate dielectric (Mylar). As engine compartments increase in complexity and air-flow is diminished, temperatures become extremely significant. All automotive products will now incorporate this new manufacturing process – Silicone Fluid Vacuum Impregnation (SFVI).
American Radionic Company re-locates from Connecticut to a new modern facility in Palm Coast, Florida.
General Motors requests that American Radionic Company assist them with a major problem in an existing model, relating to noise suppression (tape deck). Mr. Stockman flies to Detroit with Mr. Dalzell, Chief Engineer, and a vehicle is presented to them. Approximately one month after returning to Connecticut with the vehicle, the problem is solved and another new product emerges.
American Radionic Company commences the manufacture of a special, metallized polypropylene capacitor for a major U.S. corporation. This product is sold to them on a private-label basis (their logo) which they re-sell in the U.S. and other markets. This continues to operate as a highly successful arrangement. A patent is issued for an improvement in the ability to meet certain UL requirements for dry (non-liquid filled) high voltage (AC) capacitors when subjected to high fault currents (10,000 amps) Patent No. 4,633,365. After 12 years of exhaustive research covering prior technology, the Ultramet® Capacitor receives German Patent No. DE2544225C2.
The first of a group of high-profile automobiles are purchased by the Company for use as a rolling test-bed and marketing tool in a continuing effort to maintain market share in the extremely competitive worldwide automotive market. In the engineering departments (in Detroit, Michigan) considerable interest is aroused because of this program.
American Radionic Company was chosen to set up a complete AC capacitor facility for the largest manufacturer of lighting equipment in Mexico (Sola Basic, a Division of General Signal). This plant continues to operate successfully, producing millions of capacitors annually. American Radionic Company has “oversight” responsibility for this facility. Patent No. 4,558,394 – A concept which uses a system of built-in jumper wires allowing a user to select and extract different values from a single capacitor.
Responding to American Radionic Company’s efforts to improve its position with the domestic automobile industry, the state of Connecticut issues Experimental Test License Plates. These enable the Company to expand its’ highway based program of research and development in the automotive noise-suppression area.
The Unites States Patent Office issues No. 4,312,027. This patent describes a method which allows the Company to supply a multiple value with electrostatic shielding to eliminate internal interference which might cause problems in sophisticated aircraft and navigational equipment. The first large-scale market opens up for the multiple metallized capacitor. The switch networks used for adjusting the speed of overhead ceiling fans had incorporated transformers. These created an objectionable “humming” noise in the fan motors. Capacitors had been known to cure this problem but the recessed, wall-mounted boxes did not offer enough space for the cluster of capacitors and resistors needed to provide the three speeds required. The answer was found in the Ultramet® which forms the most volumetrically efficient “package” for any group of film capacitors. Patent No. 4,352,145 – Additional modification to the Ultramet®technique. Patent describes a system of producing very small values along with large values in the same winding. Very significant for use in fluorescent ballast applications.
Robert Stockman, Vice President of American Radionic Company, signs an agreement with Robert Sprague, Chairman of Sprague Electric company, the largest capacitor manufacturer in the world (at that time). Sprague agrees to pay royalties to American Radionic Company to allow them to manufacture the Ultramet® (U.S. Patent No. 3,921,041).
In an effort to support the Company’s work in the automotive field, a separate product development group is structured to monitor and improve existing components in the severe working environment of the engine compartment.
1987
American Radionic Co. relocates to Palm Coast, Florida.
1982
Robert Stockman becomes president and Richard Stockman is appointed vice-president. Edward Duarte, who has been with the company since 1964, takes over as General Manager.
1980
Electronic Products Magazine chose the multiple metallized capacitor, the Ultramet®, as one of the eighteen most significant electronic products of the year. (Note: Texas Instruments’ speech synthesizer received this award). The first commercial application of the Ultramet® Capacitor – The UAUC: this device incorporates five separate values in one single continuous winding and is sold to the appliance service industry as a replacement part for almost any value that is encountered when repairing equipment in the field. By using jumper wires and combining different values (in parallel and series), 120 different combinations of single and dual values can be duplicated.
An agreement is signed with Evomec Oy of Finland, to manufacture high-speed machinery for the production of the multiple metallized capacitor – The Ultramet®. Later, agreements are reached with Kaido Manufacturing Company, Ltd. Of Japan. As an adjunct to the multiple value metallized capacitor patented in 1975, a technique is developed to permit not only multiple values but also multiple voltage ratings from one single, continuous winding (U.S. Patent No. 4,028,595). This has a specific application in telephone handsets and related hardware.
The Pulsecap® capacitor: A new technique in winding allows the company to achieve the highest volts per mil capability of any film dielectric capacitor in the world (10,000 volts/mil) smaller and less expensive for use in heavy, pulsing applications (600V to 800V) can now be manufactured and sold.
A Technology Transfer Department was created to promote and license products which were rapidly being developed. The AC Motor-Run capacitor industry had to shift away from PCB oil impregnated paper dielectric duplicated with the metallized version. When word spread that the technology did exist to create the modern version of the dual capacitor, American Radionic Company was approached by companies throughout the world to share this invention. The capacitor was to become known by its registered trademark, The Ultramet®.
Development of the world’s first multiple metallized film dielectric capacitor produced from a single continuous winding. The technique was so advanced that the film capacitor winding equipment did not exist to produce it.
One of the first products which emerged from this effort was the Fail-Safe Capacitor, which received United States Patent No. 3,792,323. This capacitor was used in special circuitry in television sets to disrupt the high voltage to the picture tube so that there would be no excess (dangerous) radiation emitted. To help us meet the total demand, American Radionic Company licensed the Sprague Electric Company to also manufacture this product. Total volume estimated at almost $100 million in sales. This patent was later re-issued in 1977 (Re. 39,126).
American Radionic Company embarks on a product development program structured to bring new and significant products to market annually. A research group evolves and an association develops with Connecticut based patent attorneys (Parmalee, Johnson, Bollinger & Bramblett).
1966
Robert Stockman joins the firm after graduation from Rollins College. He is appointed Sales Manager and is instrumental in forming the Precision Capacitor Division which specializes in close tolerance, highly sophisticated, film dielectric capacitors. Richard Stockman becomes part of the American Radionic team after graduating from Hillsdale College and joins the Sales Department where he develops the capacitors and switch assemblies used in the overhead fan industry.
1957
American Radionic moves to larger facilities in Danbury, Connecticut where, throughout the fifties and sixties, a large part of the business is supplying capacitors to the domestic television industry and the manufacturing of noise suppression capacitors for the automotive industry.
1939
American Radionic Company, film capacitor business, is founded by William Stockman in Brooklyn, New York.